The development of modern machining technology has brought about significant changes in the mechanical engineering industry. With the advent of modern automation, precision machining in mechanical engineering is consistently carried out using advanced machinery. So, have you familiarized yourself with the sheet metal bending method? Let’s explore it together in this article with Towavina.
1. What is Sheet Metal Bending?
In the field of metal fabrication, sheet metal bending stands out as a crucial and widely applied method when processing machine components. In essence, this method focuses on shaping sheet metal according to specific requirements by folding or bending flat metal blanks. It is not only a common machining technique but also a specialized process that utilizes a bending machine to apply substantial force through a blade, thereby creating the desired curvature on one side of the sheet metal.
Throughout the sheet metal bending process, the common characteristic of the metal sheets is the necessity for flexibility and resistance to breaking. This is particularly vital for metals such as stainless steel, sheet metal, galvanized steel, and aluminum. Nowadays, the sheet metal bending process has been modernized with the introduction of advanced CNC machines. These machines are pre-programmed using computers and operate automatically, minimizing human interaction. This not only enhances efficiency but also reduces risks and ensures product quality. Let’s continue to explore the advantages and disadvantages of sheet metal fabrication services in the next section.
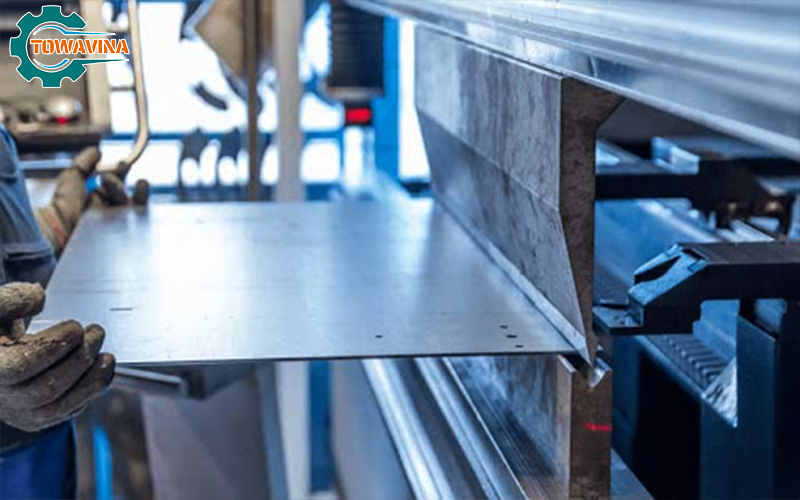
2. Advantages of Sheet Metal Bending
Sheet metal bending, facilitated by powerful machinery, enables the bending or folding of high-strength metals. Modern machines, particularly CNC bending machines, play a pivotal role in simplifying this process. CNC bending machines, with the capability to handle large metal dimensions up to 4000mm and accommodate thick and heavy sheets weighing up to 200 tons, offer a wide range of applications.
The process of sheet metal bending is not only easy but also flexible according to specific requirements. CNC machines effectively handle the bending of small and complex details. The standout feature of this process is its high and consistent precision, reaching up to 100%.
With the advantages of mass production and high productivity, sheet metal bending using CNC machines significantly enhances production efficiency. These machines can operate continuously for extended periods at high speeds, minimizing both time and manual labor while ensuring product quality.
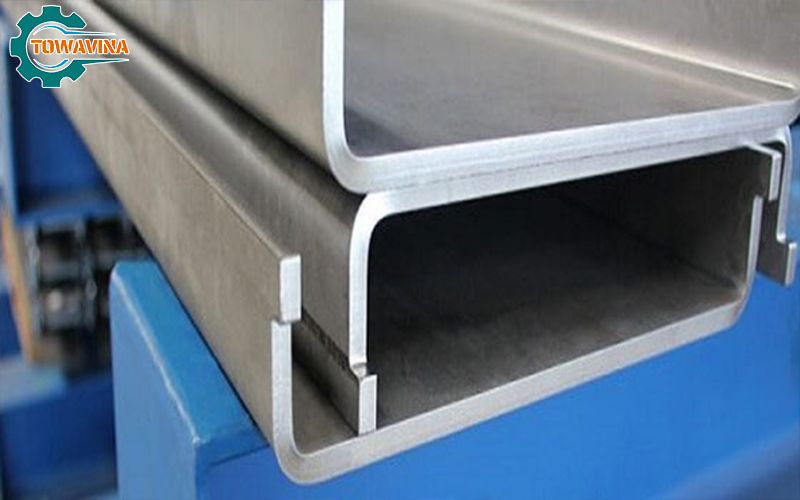
3. Disadvantages of Sheet Metal Bending
Despite the numerous benefits that sheet metal bending brings, a significant drawback is the cost associated with mold making. This is particularly challenging as the creation of molds to specifications is required before commencing the bending process. Beyond the initial expenses, the maintenance cost of molds is also a factor that needs careful consideration, posing a difficulty in sustaining an efficient production process.
Another challenge arises from the skill requirements of the machine operator responsible for sheet metal bending. Achieving precise folding lines, especially for small details and intricate angles, demands a high level of expertise and experience. This not only increases labor costs but also poses a challenge in recruiting and maintaining a high-quality workforce.
4. Methods of Sheet Metal Bending
Sheet metal bending is not just a singular process; it offers diversity with various methods catering to different bending needs. Here are four different sheet metal bending methods:
Air Bending (Free Bending): In this method, the metal is lifted, forming an angle when the bending tool presses down. What distinguishes this method is that the bending tool doesn’t press into the die, as is common in traditional methods. The depth of the bending tool directly influences the sharpness of the angle formed on the metal surface.
Bottoming: In contrast to free bending, this method requires the bending tool to completely press the metal blank into the die. This demands uniformity and precision between the bending tool and the die to create a product with a stable shape.
Edge Bending (Edge Folding, Flanging): In this form, the edge of the metal is fully pressed inside, increasing stiffness and protecting the metal details.
Roll Bending (Sheet Metal Rolling, Continuous Bending): This method transforms the sheet metal into a continuously folded C-shape. It is a relatively new technology often applied to bend very thin sheets. This bending method is fast and flexible, particularly efficient for low-volume orders.
If you are looking for metal laser cutting services on any material such as steel, stainless steel, metal, aluminum, etc., please contact us. Our team of consultants and technicians is dedicated to assisting you in achieving the desired product.
TOWAVINA CO.,LTD
Binh Chuan 44, Binh Chuan, Thuan An, Binh Duong
Hottline: 0979.034.634 – 0931.155.155
Mail: sales@towavina.com
Website: towavina.com