The CNC plasma cutting machine is widely used in precision mechanical processing industries today. Operating by using a high-temperature plasma torch to cut various metal materials such as iron, steel, stainless steel, copper, and aluminum, this machine is effectively applied in machinery manufacturing, mechanical industries, and agricultural equipment repair. However, as this machine utilizes modern technology, many might not be familiar with its basic information. In this article, Towavina will help you gain a better understanding of the CNC plasma cutting machine.
Understanding the CNC Plasma Cutting Machine
The CNC plasma cutting machine operates by heating the surface of the metal to be cut using a plasma cutting torch to create precise cutting lines. Equipped with an automatic control system through computer software, this machine enables quick and easy cutting processes.
The CNC plasma cutting machine can process metal materials such as steel plates, aluminum, iron, stainless steel plates, copper, etc. Using the plasma cutting method helps create products with high precision, beautiful and sharp cutting lines. Moreover, it minimizes labor for manufacturers in subsequent stages.
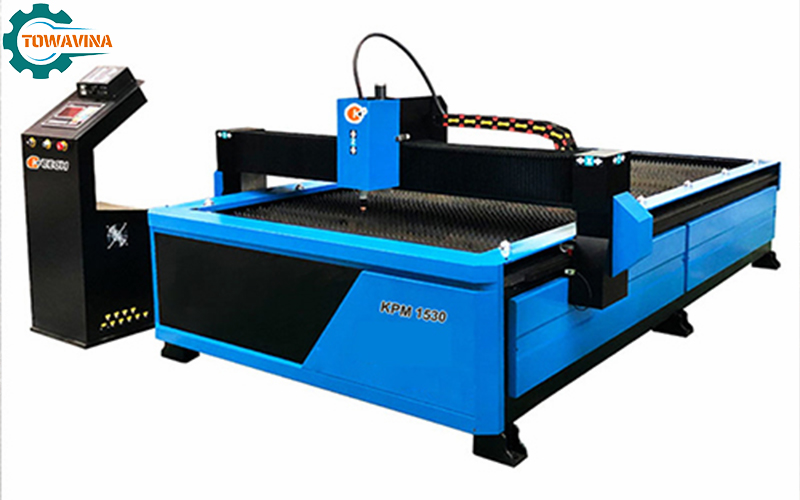
Working Principle of Plasma Machines
To start the cutting machine, the cutting torch assembly of the machine needs to be connected to the positive pole of the power source and the material being processed to the positive pole of the power supply. Once the metal is melted, a stream of air will be released. Electric sparks will be propelled through the nozzle inside the cutting head to form a plasma arc. This arc will shine on the material, conducting electricity to the positive pole of the power supply.
The high temperature of the plasma arc will swiftly melt the metal surface, creating the cutting line. The CNC Plasma Cutting Machine will move the cutting head along the pre-programmed pattern in the design drawing. To ensure the stability of the nozzle with the material surface, this cutting machine has control sensors.
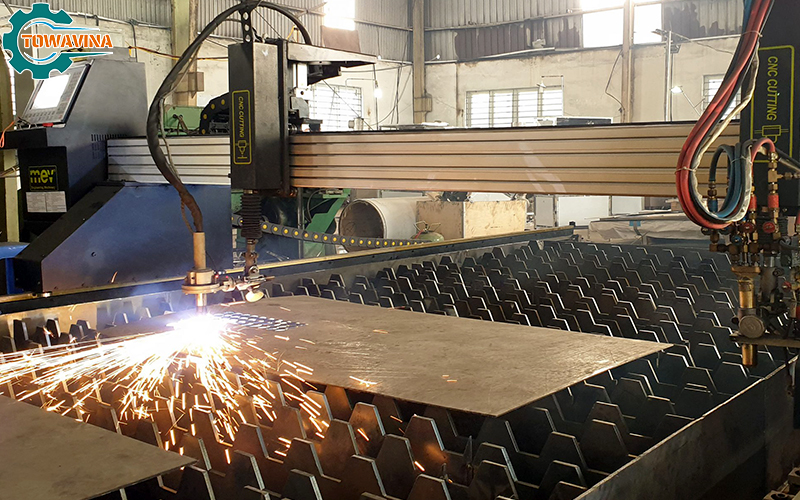
Operating Notes in Mechanical Processing
To ensure safety when operating the CNC Plasma Machine, adhere to these rules: wear full protective gear such as goggles, gloves, and masks. Before cutting, check the perpendicularity of the cutting nozzle with the machine. To minimize smoke and dust, pump enough water when performing plasma cutting. To avoid product deformation, ensure the cutting direction and sequence are correct. Avoid immersing the Plasma source in water. Regularly check the cutting torch and electrodes to prevent damage to the cutting nozzle. Do not use grease on the rack and guide rails.
Regularly drain water from the air compressor tank and water separator. When using Plasma or Oxy Gas, use the correct cutting nozzle for the best cutting line. Ensure stable power supply. Adjust Plasma cutting parameters according to the material thickness. Clean the machine daily and after operation. Upon completing the processing, perform these actions: turn off the CNC machine, shut down the Plasma power, and close the valves of compressed air and Oxy Gas to ensure fire safety.
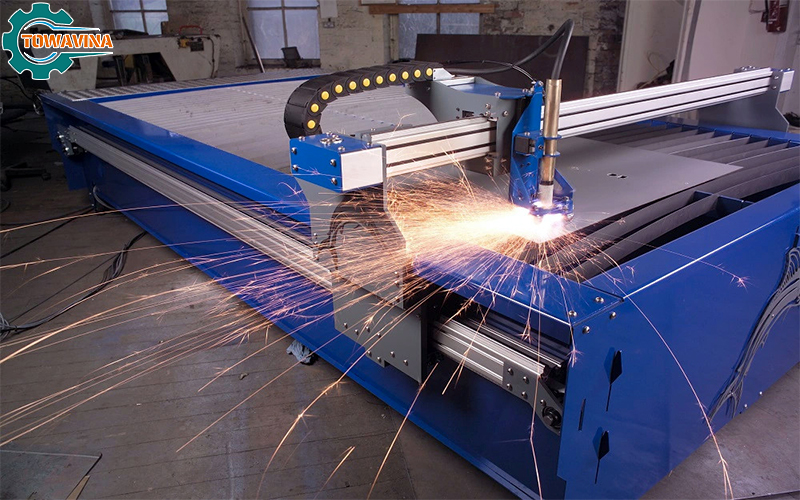
Advantages of CNC Plasma Cutting Machine
The method of metal cutting using a Plasma machine offers a range of significant advantages to users. Not only is it capable of cutting materials much faster than traditional methods like sawing or oxy-gas, but it also plays an increasingly vital role in industry and economics.
A notable feature of CNC plasma machines is their ultra-fast cutting speed, thanks to the operating principle based on a plasma airflow. Metals with high hardness make machining intricate. The extremely rapid cutting speed of this machine is the decisive factor in avoiding damage to metal blanks. Operators need to work swiftly and continuously to ensure accuracy and efficiency.
Compared to oxy-gas metal cutting machines, plasma machines cut much faster, handling metal sheets up to 50 mm thick. For thin metal blanks under 3 mm, using a CNC plasma machine instead of a laser cutter is a more practical choice.
Plasma cutting machines are also user-friendly and don’t demand operators with advanced skills. This helps produce products with smoother and more aesthetically pleasing cutting lines.
Economically, plasma cutting machines offer higher efficiency compared to traditional cutting methods. Low initial investment costs coupled with superior metal cutting performance increase profitability for businesses.