Metal sheet laser cutting is a widely popular method, particularly in the realm of mechanical engineering and manufacturing. How is the process of metal sheet laser cutting formed? Let’s delve into it with Towavina in this article.
1. What is Metal Sheet Cutting and Shaping?
The process of cutting and shaping metal sheets involves manufacturing metal products used in household appliances and electronic devices industries. The raw material comprises pressure-rolled metal sheets, flattened into rectangular shapes, with an average thickness ranging from 4-6mm or more. Cutting and shaping processes are carried out directly on these cold metal sheets.
2. The Metal Sheet Laser Cutting Process
The laser cutting of metal sheets has undergone several developmental stages before this cutting-edge technology emerged.
- Blade cutting: This method was extensively used in the initial phase of metal cutting. Presently, it’s less utilized and primarily for rough metal cuts. Within the blade cutting machine, there are two blades—one fixed below and one moving along a straight path to cut the metal.
- Advanced metal cutting technology: Widely used today, it includes laser cutting, plasma cutting, and waterjet cutting. This new cutting technology provides higher productivity, optimal precision, and versatility across various materials. The cuts from this technology are smoother, less burr-prone, and capable of intricate shapes.
Currently, laser metal cutting is widely employed due to its time and labor efficiency, concurrently enhancing the quality of processed products.
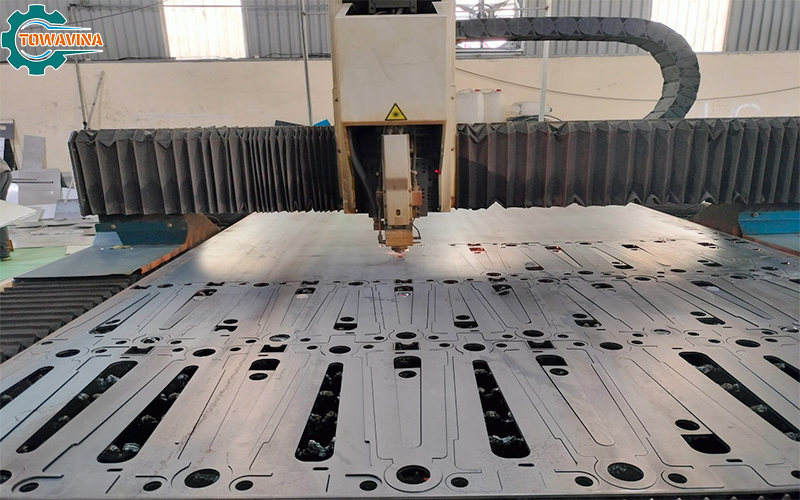
3. The Process of Shaping Metal Sheets
The metal sheet forming process, also known as CNC bending, is a method of reshaping metal beyond its ductile limit to form desired angles without causing cracks or fractures. The bending force applied must exceed the metal’s ductile limit but remain below its tensile strength. Typically, metal sheet forming and laser cutting processes are executed simultaneously to achieve the highest-quality metal products.
4. The Principles of Metal Sheet Laser Cutting
The process of cutting metal with a laser operates on the following principles:
- A laser beam is emitted from a high-energy source, generating high temperatures. Through a system of converging lenses, the laser beam is focused onto the surface of the metal sheet to be processed.
- The concentrated laser beam burns and heats the metal sheet at the cutting position. Subsequently, a high-pressure gas stream is used to blow the molten metal away from the sheet, creating a smooth and aesthetically pleasing cut surface as per the required specifications.
Typically, a laser cutting machine is pre-programmed, and during operation, the cutting follows the predetermined design programmed into the machine.
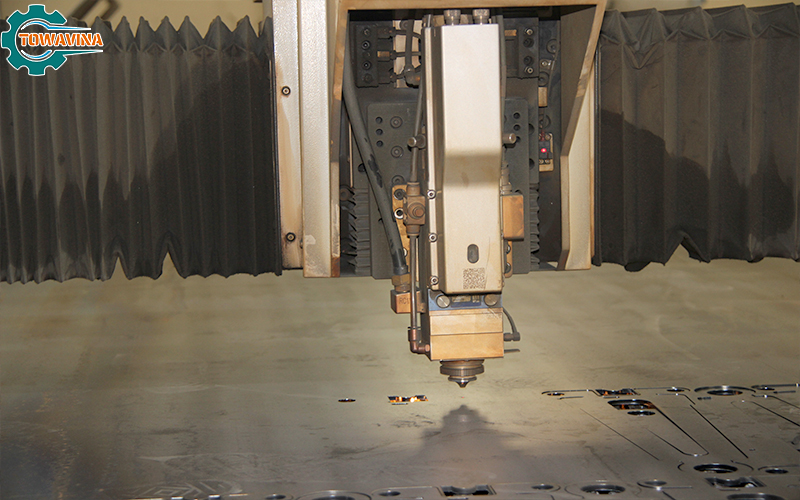
5. Advantages and Disadvantages of Metal Laser Cutting
+) Advantages
- Laser cutting technology is exceedingly fast and flexible.
- With this technology, various metal types of different thicknesses can be cut and shaped into diverse forms: from straight lines to curved shapes, making virtually any design feasible.
- The capability to cut intricate details, demanding high precision, is a hallmark of laser cutting technology.
- The resulting cuts are smooth, compact, and incredibly precise, ensuring not only high-quality products but also a high aesthetic appeal.
- Particularly noteworthy is the extremely low error rate, and metals maintain their shape after the cutting process.
- Utilizing pre-programmed CNC laser cutting machines not only saves time but also mitigates unwanted noise.
+) Disadvantages
- Operating laser cutting machinery requires substantial costs and demands operators with strong technical expertise.
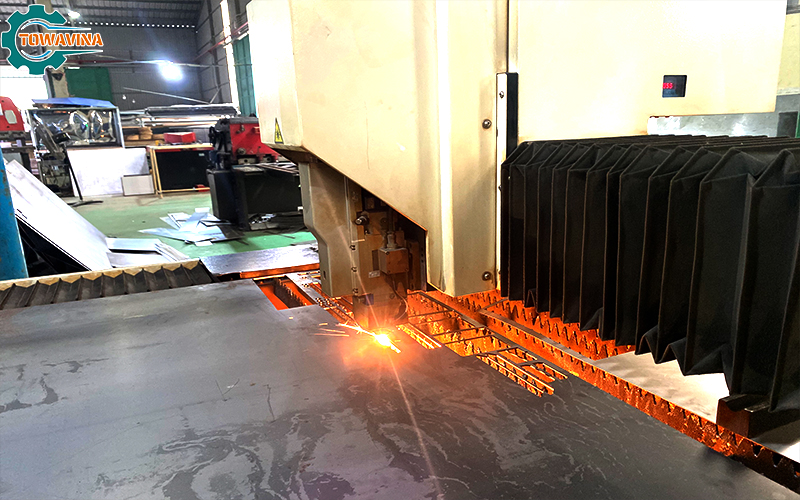
6. Metal Machining Services at Towavina
Towavina continuously strives to offer customers the finest quality services, ensuring finished products without the need for various machining stages from different facilities. Our dedication and commitment are paramount in providing the utmost satisfaction to our customers. We provide premium services such as CNC bending, laser cutting, milling, and turning.
For detailed service inquiries, please contact us. Our team of consultants and technicians is dedicated to assisting you in achieving the desired product.
TOWAVINA CO.,LTD
Binh Chuan 44, Binh Chuan, Thuan An, Binh Duong
Hottline: 0979.034.634 – 0931.155.155
Mail: sales@towavina.com
Website: towavina.com