Precision mechanical machining is a widely implemented machining method using CNC machines today. So, what exactly is precision mechanical machining? What are its advantages and disadvantages? Let’s delve into this machining form with Towavina in the following article.
1. What is Precision Mechanical Machining?
Precision mechanical machining, also known as CNC machining, utilizes modern equipment and high-precision machinery such as milling machines, lathes, and high-speed robots to operate. Materials commonly used in precision mechanical engineering include glass, steel, graphite, lead, stainless steel, and plastics.
The most significant difference between precision mechanical machining and other machining types lies in the utilization of various modern machinery and equipment, enabling products to achieve nearly absolute precision.
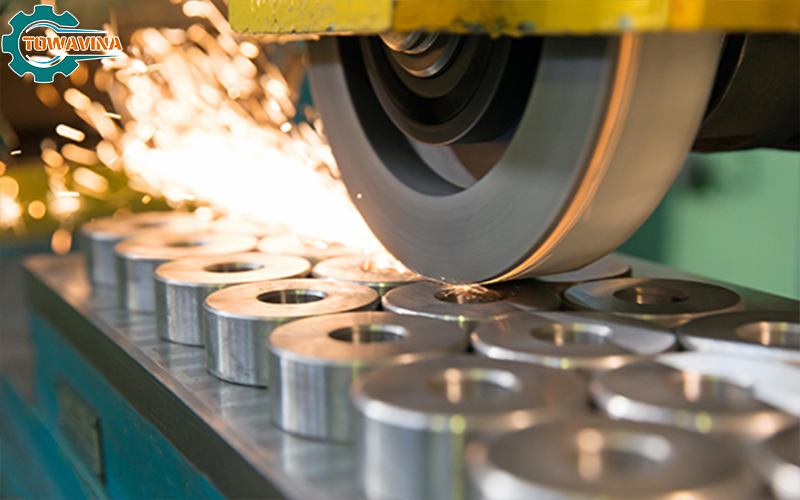
2. Advantages of Precision Mechanical Machining
It doesn’t demand excessively hard materials during the machining process. It can work with most materials, especially those with high hardness. The surface of the product after machining exhibits much smoother finishes and significantly higher dimensional accuracy compared to mechanically processed mechanical products using alternative methods. CNC milling and turning methods can produce highly intricate and precisely accurate products, particularly when machining spirals using 3-axis CNC lathes and 4-5-axis CNC milling machines.
The most outstanding advantage of precision mechanical machining is its capability to process almost all types of materials with minimal mechanical force applied.
3. Disadvantages of Precision Mechanical Machining
To execute precision mechanical machining, the operator needs specialized knowledge of equipment and machinery to ensure operational efficiency. CNC machines are usually robust but expensive to repair in case of malfunctions. Additionally, controlling the machine can be challenging if the operator is busy or requests time off.
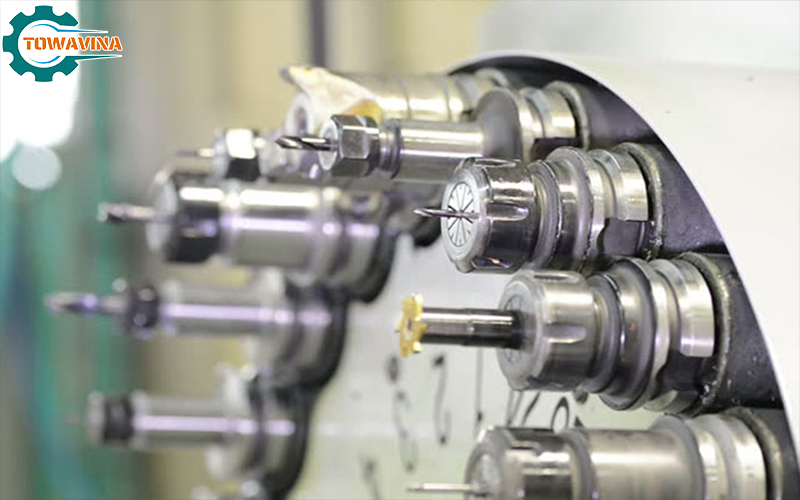
4. Contemporary Precision Mechanical Machining Methods
4.1. CNC Milling
CNC milling involves using rotating cutting tools to machine materials. Metal products are shaped using multiple cutting blades through two movements: the rotational milling cutter and three-axis linear movement. CNC milling machines can cut various materials like iron, steel, aluminum, stainless steel, titanium, and process complex flat surfaces, curved surfaces, as well as shell components like molds, connectors, drives, cutting blades, machine casings, and machine components.
4.2. CNC Turning
CNC lathes operate similarly to CNC milling but are used to produce cylindrical metal products. Cutting tools lightly touch the product as it rotates, removing excess material to shape the product.
Turning methods play a crucial role in metal cutting and shaping. With superior features, users interact between the stock and the turning tool. CNC lathes are often used to process complex rotating surfaces like linear cylinders, inclined or hyperboloid cylinders, and other threads. It can produce various products, from simple to complex parts like machine details, solid shapes, chamfers, beveled corners, and gear cutting.
The primary operation principle of turning machining relies on the efficient circular motion of the stock to create cutting motion, including the linear movement of composite tools, comprising both vertical and horizontal cutters. Due to its critical role in machining, most manufacturing workshops, from small to large, currently utilize lathes. Statistics show that approximately 25-35% of all equipment in modern cutting workshops are dedicated to lathes to assist in their processes.
4.3. CNC Drilling
CNC drilling is the process of using drill bits to create holes in metal surfaces and other materials. The drill bit has extremely high precision, operates continuously, and reduces execution time. The depth of the drill hole is adjusted according to preset programs.
CNC drilling technology with high accuracy is commonly used to create holes on product surfaces as per manufacturing requirements.
4.4. Grinding Machining
CNC grinding machining is performed using CNC technology to flatten the surface of materials, especially those with high hardness like alloys, steel, and even those with high brittleness like granite or glass. CNC grinding machines smooth, abrade, remove excess materials, and polish to create aesthetically pleasing surfaces.
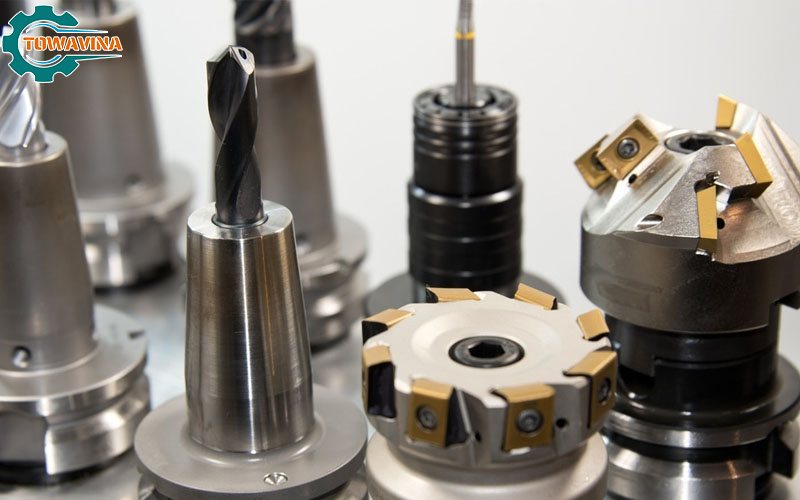
4.5. Gear Cutting Machining
CNC gear cutting machining utilizes CNC water jet cutting machines combined with milling, profiling, tooth cutting, etc., to create machine gears, ensuring hardness and precision as per the blueprint. This method is applied across all machinery gear production, automobiles, gear shafts, and gear wheels in mechanical machines.
4.6. CNC Planing
CNC planing machining is used to thin the product surface and create a beautiful, smooth surface with appropriate thickness according to design requirements. This method is commonly applied in the production of wooden products or machine casings.
4.7. Broaching Machining
CNC broaching machining is the process of enlarging existing holes on materials using cylindrical or tapered broaching tools. To ensure accuracy, broaching tools are made from wind steel, Fe-Co alloys, and carbide (hard alloy) with precise cutting abilities. However, it’s not recommended for machining with significant surplus material.
This method can be applied to expand through-holes with straight centerlines and unchanged cross-sections. If the hole requires high concentricity and precise tolerances, pre-drilling or point drilling is needed, followed by regular drilling, rough broaching, and final broaching for completion.
Applications include machining shaped holes, round holes, threads, flower-shaped threads, or flat surfaces, outer cylindrical surfaces, and spiral grooves.
4.8. Sawing Machining
CNC sawing machining technology is applied to cut parts as per blueprints with high precision and speed. This method is also used to create curves in materials.
4.9. Plasma and Laser CNC Mechanical Machining
Plasma and Laser CNC mechanical machining use high-energy and temperature beams to cut metal surfaces. This process is fast and generates sharp, non-rough or blackened cuts.
This method is used to cut simple to complex parts with high precision without the need for reprocessing. It is also applied in artistic architectural machining for intricate engravings and creating V-shaped angles.
Conclusion
This article aims to provide insights into 9 contemporary precision mechanical machining methods. Hopefully, this information helps you choose the most suitable CNC machining method for your needs. For detailed service inquiries, please contact us. Our team of consultants and technicians is dedicated to assisting you in achieving the desired product.
TOWAVINA CO.,LTD
Binh Chuan 44, Binh Chuan, Thuan An, Binh Duong
Hottline: 0979.034.634 – 0931.155.155
Mail: sales@towavina.com
Website: towavina.com